Decarbonation of cement: a necessary transition and innovative solutions
The cement industry is currently facing a major challenge: reducing its carbon footprint. Responsible for around 7% of global greenhouse gas (GHG) emissions, cement production has traditionally been based on clinker, a component obtained by firing a mixture of limestone and clay at very high temperatures (1,450°C). This extremely energy-intensive process generates significant CO₂ emissions, due to the combustion of the fossil fuels needed to heat and decarbonate the limestone.
High performance alternative for greener cement
In response to environmental challenges, alternative solutions have been developed to reduce dependence on clinker, by incorporating mineral additives such as :
- Limestone: used to formulate CEM II and CEM III cements, reducing the proportion of clinker.
- Blast furnace slag: a by-product of the steel industry, which improves the durability and strength of cement.
- Natural and artificial pozzolans: siliceous and aluminous materials that react with lime to form hydraulic compounds, improving mechanical performance.
- Calcined clays (metakaolin, thermally transformed clays): a promising alternative with a low carbon impact and interesting reactive properties.
As well as reducing environmental impact, these materials offer mechanical and chemical properties that are often comparable or even superior to those of clinker. Their widespread adoption represents a key lever for decarbonising the cement industry. However, their implementation requires significant technical and financial adjustments for the players in the sector.
POITTEMILL is your partner in the low-carbon transition
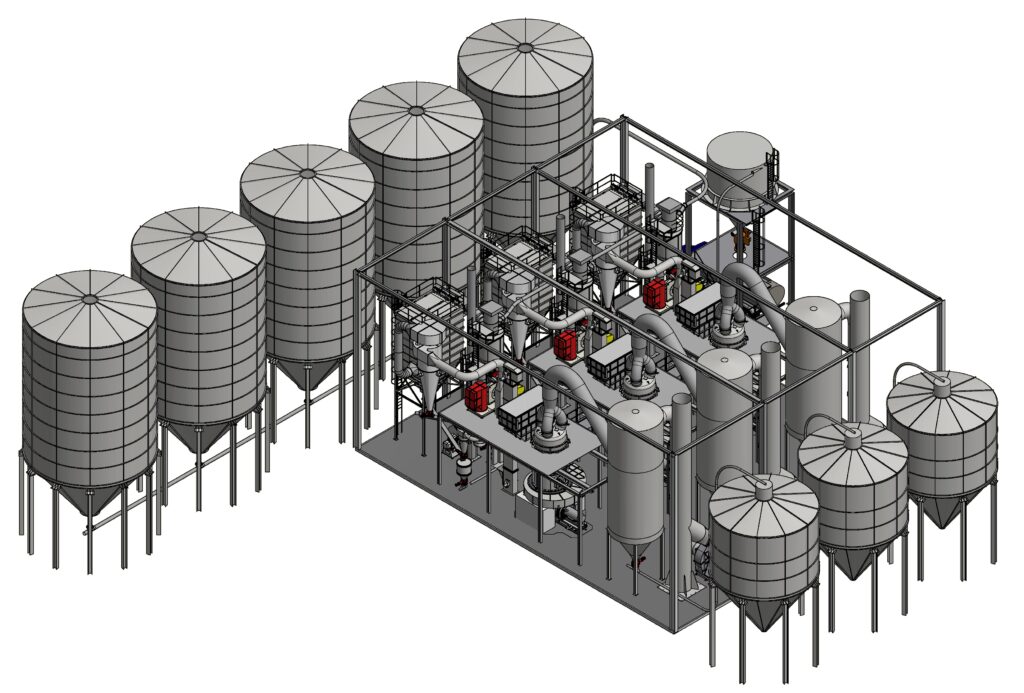
As a specialist in grinding and classification processes, POITTEMILL supports the mineral industry in this transformation thanks to its expertise and equipment adapted to the new challenges of cement production.
Grinding-drying and separation equipment: technologies capable of micronising abrasive materials (slag, pozzolans, calcined clays) while guaranteeing low energy consumption and high production rates.
Process engineering expertise: integration and design of complete production lines adapted to new low-carbon cements.
A dedicated test station: enabling us to test, optimise and validate the performance of our processes before they go into production, thereby reducing technical and financial risks.
Thanks to its advanced technologies and recognised expertise, POITTEMILL is helping cement manufacturers to meet the challenges of the energy transition and adopt more environmentally-friendly processes.
Innovation and optimisation of manufacturing processes are essential steps in building a sustainable and competitive cement sector. POITTEMILL has positioned itself as a key partner in supporting these developments and meeting the demands of tomorrow’s construction.
Complete process engineering
- Consultancy (optimisation, energy, maintenance, etc.)
- Granulometric testing and analysis
- Design, supply and commissioning of complete powder preparation facilities, including all or part of the following sectors
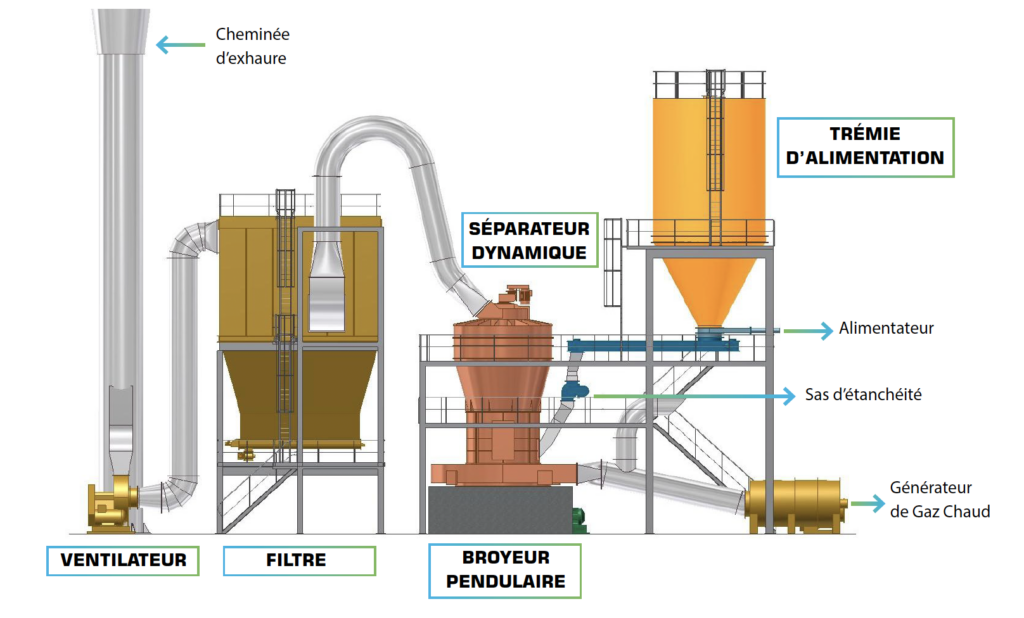
CONTACT US
A project ? An information ?
At the cutting edge of innovation, the POITTEMILL Group has been designing its own equipment for over 90 years, offering customised turnkey solutions.