Complete Guide to Grinding, Milling, and Particle Size Reduction Terminology
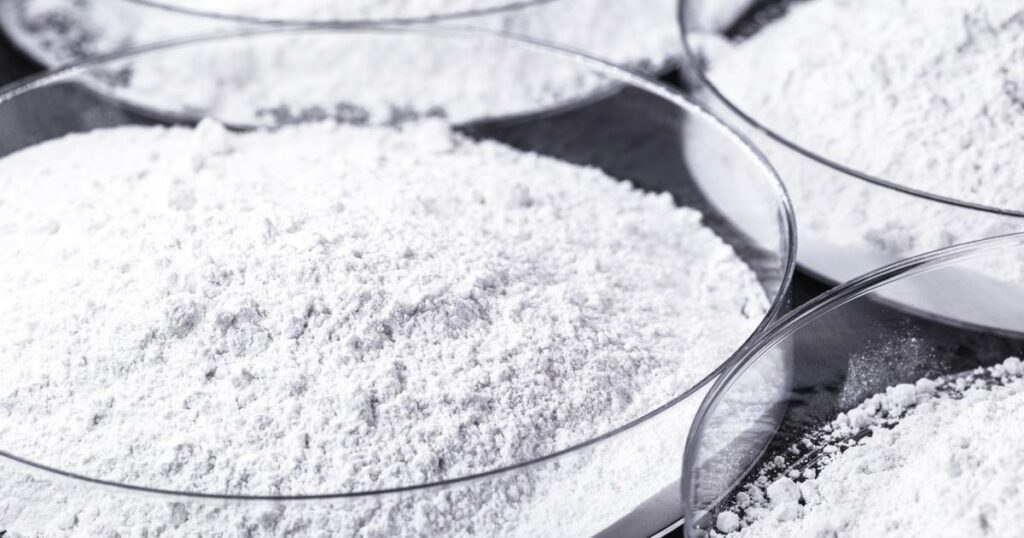
Grinding and particle size processing
Abrasiveness
Abrasiveness is related to hardness and significantly impacts the wear of mill components. Materials such as pyrite, coke, quartz, and silica are known for their high abrasiveness.
Feed
The term feed refers to the particle size of materials introduced into the mill inlet. The feed size is contrasted with the output, representing the particle size exiting the mill.
Energy Consumption
Energy consumption during milling is considerable and increases with desired fineness. For dry milling, energy consumption can rise by up to 30%, but this advantage is offset if the product requires subsequent drying or deagglomeration.
Density
Density, for a solid, is the mass of one liter of the material. It primarily affects handling and storage and plays an essential role in milling efficiency.
Hardness
Hardness is defined relative to another material. A solid is harder than another if it can scratch it but not be scratched by it. The commonly used hardness scale is the Mohs scale:
- 1. Talc: Magnesium silicates
- 2. Gypsum: Sulfates
- 3. Calcite: CaCO3 limestone, aragonite
- 4. Fluorine
- 5. Apatite: Phosphates
- 6. Orthoclase: Feldspars
- 7. Quartz: Silica
- 8. Topaz: Accessory silicates
- 9. Corundum: Oxides
- 10. Diamond: Native metalloids
D50, D95
D50 represents a diameter where 50% of the grains by weight are smaller, while D95 signifies a diameter where 95% are smaller by weight.
Grinding Energy
The grinding energy equation is represented as E = k (1/d - 1/D)
, where k
depends on the product and mill. Grinding energy is proportional to the new surfaces created, although calculation remains variable. Grinding energy is generally low, around 3% of the total energy required by the milling setup, primarily due to friction and solid transport energy.
Friability
Friability, unrelated to hardness, describes how easily a substance breaks on impact. For instance, coal and diamond are friable, while plastics are not.
Particle Size Distribution
Particle size distribution involves measuring particle sizes in substances like flour, powders, and sands. For milled products, particle sizes are determined within ranges (e.g., <10µm, 10µm
HARDGROVE Grindability Index
The HARDGROVE Grindability Index quantifies a sample’s grindability. Lower indices indicate harder materials. A sample of 50g is loaded into a HARDGROVE mill for 60 rotations, followed by sieving at 200 mesh (74 microns). The index is calculated as:
I = 13 + (weight of passing material in grams x 6.93)
Reduction Ratio
The reduction ratio (n) is given by n = D/d
, where D
is the initial and d
the final characteristic dimension. Equipment is specialized for certain reduction ratio ranges. For example, reducing ore blocks from 30cm to 0.4mm fragments requires a ratio of 750, achievable in three stages: crushing to 3cm, granulation to 6mm, and milling to 0.4mm.
Specific Surface
The specific surface denotes total surface area per mass unit accessible to atoms and molecules. Expressed in cm²/gram, specific surface area is essential for characterizing powders or solids in various applications, such as catalysts, pharmaceuticals, PVC, etc.
Sieving
Sieving classifies grains by size, passing them through decreasing aperture sizes. Each refusal and final sieve fraction is weighed, providing weight per size class. A vacuum-assisted sieve system increases effectiveness.
Moisture Content
The moisture content is determined by placing a 100g product sample in an oven for 3 hours, then weighing it again. The moisture rate is the mass difference over the initial weight. Typically, moisture should be 1-4%, as higher levels risk clogging.
Dry or Wet Process
Dry processing involves milling in dry conditions, preferred if the product requires subsequent drying or to avoid agglomeration. Wet processing is used when the product is wet or will remain so.
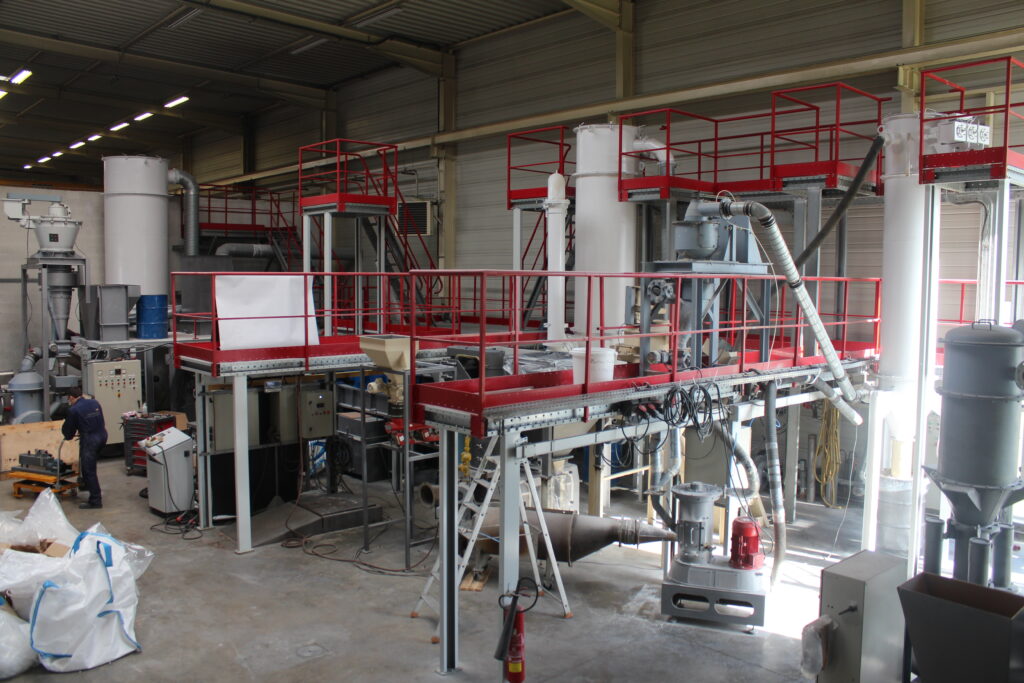
Benefit from the advice of the POITTEMILL Group, experts in powder processing, drying and classification technology.
Our laboratory and testing centre offers numerous opportunities to test machines, parameters and processes, at both pilot and full scale, to ensure that the quality of your products and the efficiency of your operations generate maximum return on investment for your business.
CONTACT US
A project ? An information ?
At the cutting edge of innovation, the POITTEMILL Group has been designing its own equipment for over 90 years, offering customised turnkey solutions.