Glossaire lié au broyage
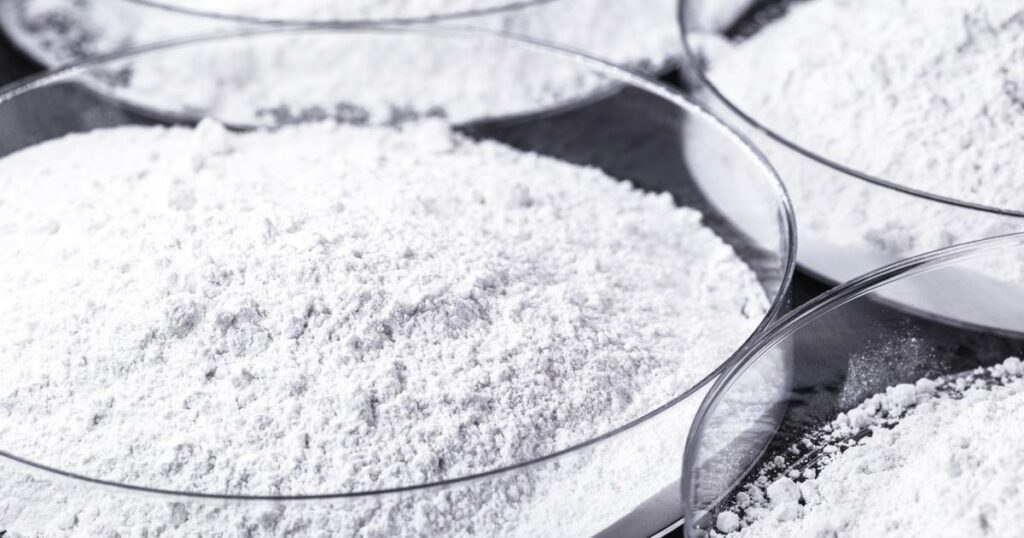
Broyage et traitement des poudres
- Abrasivité : elle est en relation avec la dureté et a surtout une influence sur l’usure des organes du broyeur. La pyrite, le coke, le quartz, la silice sont très abrasifs.
- Alimentation : appellation donnée à la taille des particules qui sont insérées en entrée de broyeur. L’alimentation s’oppose à la sortie, correspondant logiquement à la taille des particules sortants du broyeur.
- Consommation d’énergie : La consommation d’énergie lors d’un broyage est importante, et augmente avec la finesse désirée. Lors du broyage à sec, la consommation énergétique supplémentaire peut atteindre 30%, mais l’avantage du broyage humide est perdu si le produit doit ensuite être séché ou désaggloméré.
- Densité: Pour un solide, correspond à la masse d’un litre du matériau. Elle conditionne principalement la manutention et le stockage des matériaux et joue un rôle important dans le rendement du broyage ou de la selection.
- Dureté : elle est définie par rapport à un autre matériau. Un solide est plus dur qu’une autre si il le raye et nest pas rayé par lui.
L’échelle de dureté couramment utilisée est l’échelle de MOHS :
- Talc, silicates magnésiens
- Gypse, sulfates
- Calcite, calcaire de CaCO3, aragonite
- Fluorine
- Apatite, phosphates
- Orthose, feldspaths
- Quartz, silice
- Topaze, silicates accessoires des roches
- Corindon, oxydes sénaires
- Diament, métalloïdes natifs
- D50, D95 : Par « diamètre moyen D50 », on entend un diamètre tel que 50% des grains en poids on une taille inférieure audit diamètre ; par « diamètre D95 », on entend une valeur telle que 95% des grains en poids ont une taille inférieure à ladite valeur.
- Énergie de broyage : E = k (1/d – 1/D)
k dépend du produit et du broyeur.
L’énergie de broyage est proportionnelle à la somme des nouvelles surfaces crées au cours de l’opération. Mais son calcul reste aléatoire. il faut noter que l’énergie du broyage est faible ( environ 3%) devant l’énergie nécessaire à l’ensemble de l’installation de broyage, notamment en raison des frottements et de l’énergie nécessaire au transport des solides.
- Friabilité : sans rapport avec la dureté, c’est la facilité avec laquelle une substance est brisée par percussion. Le charbon et le diamant sont des substances friables, les matières plastiques ne sont pas friables.
- Granulométrie : La granulométrie a pour objet la mesure de la taille des particules élémentaires qui constituent les ensembles de grains de substances diverses, telles que les farines, poudres, sables, etc.., et la définition des fréquences statistiques des différentes tailles de grains dans l’ensemble étudié. Dans le cas d’un broyat, il s’agit de déterminer le diamètre des grains issus du broyat, par intervalles de diamètre (<10µm, 10µm<x<50µm…)
- Indice de broyabilité HARDGROVE : indice exprimant la facilité à broyer un échantillon. Il est défini par rapport à un échantillon témoin traité dans le même appareil, auquel on a attribué la broyabilité 100. Cet indice est d’autant plus faible que la matière est plus dure. Pour le déterminer on prélève un échantillon de 50g d’un produit de granulométrie préalablement mesurée. On charge alors cet échantillon dans un petit broyeur spécial HARDGROVE. Après 60 tours accomplis, le produit est tamisé à 200 mailles (74 microns). L’indice de broyabilité HARDROVE est défini par :
I = 13 + poids du passant en grammes x 6,93.
- Rapport de réduction : n=D/d
(avec D dimension initiale caractéristique, et d dimension finale caractéristique)
Chaque appareil est spécialisé pour une gamme de rapport de réduction déterminée. Si l’on souhaite réduire un minerai don les blocs font 30 cm en fragments de 0.4 mm, le rapport de réduction vaut 300/0.4 = 750, ce qui est trop élevé pour être réalisé dans un seul appareil. on opérera donc par exemple en 3 étapes :
- concassage pour fournir des fragments de dimension moyenne 3 cm
- granulation pour fournir des particules de 6mm
- broyage pour obtenir la dimension finale de 0.4mm.
- Surface spécifique : représente la surface totale par unité de masse du produit accessible aux atomes et aux molécules. C’est la surface d’un gramme de produit dont tous les grains seraient développés. Elle s’exprime en cm2/gramme. La connaissance de la surface spécifique, appelée aussi aire massique, est d’une grande importance dans la caractérisation d’un poudre ou d’un solide, quels que soient les domaines d’application : catalyseurs, produits pharmaceutiques, PVC, noir de carbone, charbon actifs..
- Tamisage : Le tamisage consiste à répartir les grains d’un échantillon en une série de classes dimensionnelles de plus en plus petites, par passage à travers des orifices de plus en plus étroits. Les refus successifs et l’ultime tamisat sont pesés, l’analyse fournit donc le poids et non le nombre de grains de chaque classe dimensionnelle. En réalité, lorsque les grains ne sont pas sphériques, les orifices les trient selon leur largeur et non selon leur longueur. Pour plus d’efficacité on relie le tamis à un système d’aspiration, qui crée une dépression et facilite le tamisage.
- Taux d’humidité : Pour déterminer ce taux, on met 100g de produit à l’étuve pendant 3 heures environ. Une pesée après cette étape donne une nouvelle masse. Le taux d’humidité correspond à la masse d’eau évaporée (différence de masse) sur la masse initiale. Un taux d’humidité généralement admis est de 1 à 4%. Au delà, il y’a un risque de formation de pâte avec blocage du broyeur.
- Voie sèche ou voie humide : La voie sèche correspond à une façon particulière de broyer, qui s’effectue à sec. La voie humide est utilisée lorsque le produit se présente à l’état mouillé ou si il sera utilisé humide. La voie sèche est préférée si le produit doit ensuite être séché, et également pour éviter son agglomération.
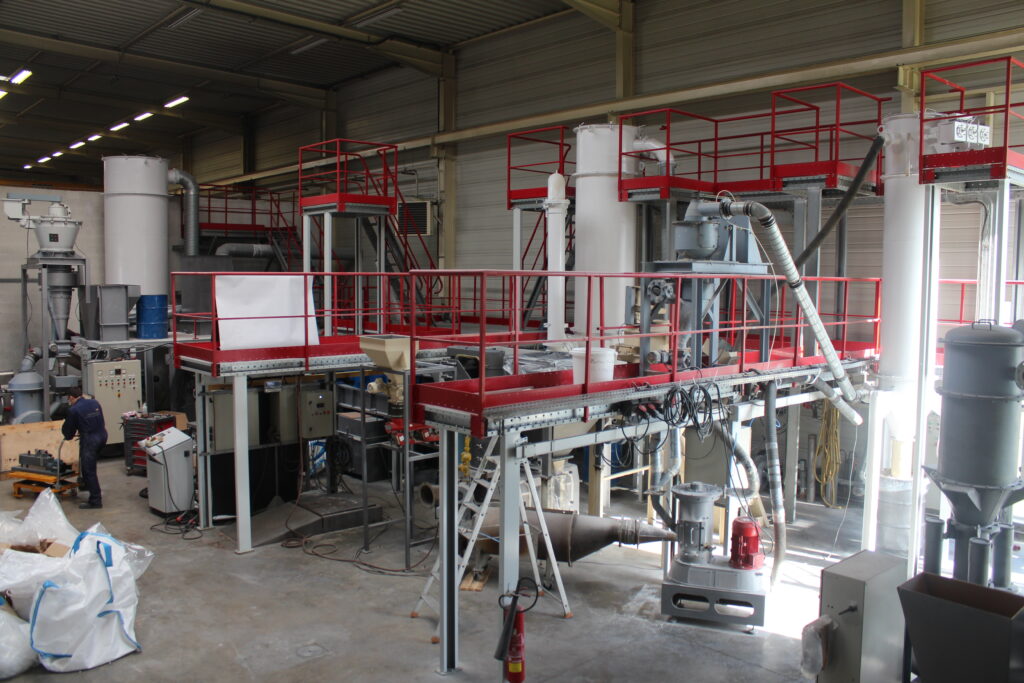
Profitez des conseils du groupe POITTEMILL, expert en technologie de transformation, de séchage et de classification des poudres.
Notre laboratoire et centre d’essais offre de nombreuses possibilités de tester les machines, les paramètres et les processus, à l’échelle pilote et à l’échelle réelle, afin de garantir que la qualité de vos produits et l’efficacité de vos opérations génèrent un retour sur investissement maximal pour votre entreprise.